Вопросы: 1.Определение термической обработки стали и чугуна - термической обработки стали и чугуна называют процессы теплового воздействия по определенным режима с целью изменения структуры и свойств сплава. 2.Назовите основные факторы термической обработки? -температура, время, скорость нагрева и охлаждения. 3.Объясните понятие слова: Диффузия -диффузия – этоперемещение адсорбированных атомов вглубь изделия 4.Назовите виды термической обработки металлов? - собственно термическая обработка; химико-термическая обработка; термомеханическая обработка. 5. С какой целью проводится термическая обработка? -для изменения механических свойств стали (прочности, твердости, пластичности, вязкости). 6.Назовите основные виды термической обработки стали. -отжиг, закалка, отпуск. 7. Чем отличаются между собой отжиг, закалка и отпуск? -температурой нагрева, временем выдержки и способом охлаждения (вместе с печью или на воздухе). Тема: Химико-термическая обработка стали Группа делится на четыре подгруппы. Каждая подгруппа подробно изучает один из видов химико-термической обработки: 1 группа – цементацию, 2 группа – азотирование, 3 группа – нитроцементацию, 4 группа – диффузионную металлизацию. Обучающиеся изучают виды химико-термической обработки стали по плану, записывая ответы в тетрадь, и составляют презентации. План составления презентации Определение Цель Ход процесса (среда, температура, время) Преимущества, недостатки В ходе урока включаются слайды презентации. После просмотра презентации студенты заполняют таблицу (приложение 1). - Вопрос: Чем термическая обработка стали отличается от химико-термической? Химико-термической обработкой называется процесспредставляющий собой сочетание термического и химического воздействия. Химико-термическая обработка предназначена для повышения твёрдости, износостойкости в поверхностных слоях при сохранении вязкой сердцевины. Химико-термическая обработка основана на диффузии, т.е. проникновении в сталь атомов различных элементов. Существует несколько видов химико-термической обработки сталей. Насыщение поверхностного слоя детали углеродом называют цементацией, азотом — азотированием, одновременно углеродом и азотом — нитроцементацией, металлом — диффузионной металлизацией. Толщина диффузионного слоя зависит от:температуры нагрева, продолжительности выдержки при насыщении, концентрации диффундирующего элемента на поверхности. После процесса диффузии детали могут быть сразу готовы к использованию или должны подвергаться дополнительной Цементация (презентация) Цементация - процесс химико-термической обработки, представляющий собой диффузионное насыщение поверхностного слоя стали углеродом при нагреве в соответствующей среде (древесный уголь, природные газы и др.). Цель цементации — получить высокую поверхностную твердость и износостойкости при вязкой сердцевине, что достигается обогащением поверхностного слоя стали углеродом в пределах 0,8-1,0% и последующей термической обработкой.Цементации подвергают детали, изготовленные из малоуглеродистых сталей (0,1...0,3 % С) марок 10, 15, 20 или легированных малоуглеродистых сталей 15Х, 20Х, 18ХГТ и др. После цементации производят закалку изделия. Цементацию проводят в твердых и газообразных и жидких углеродсодержащих средах. Цементация в твердой среде (карбюризаторе) состоит в следующем. Карбюризатором служат мелкие куски древесного угля, покрытые углекислыми солями бария и натрия, которые ускоряют процесс цементации. Детали помещают в специальный стальной ящик, засыпают со всех сторон карбюризатором и ящик накрывают крышкой. Расстояние между деталями и стенками ящика должно быть не менее 10...15 мм. Чтобы не было доступа воздуха, разъем ящика обмазывают глиной. Затем ящик, помещают в термическую печь и нагревают до Т=900...950°С Выдержка 7...10 ч. Толщина слоя0,7..,1,5 мм. При этой температура древесный уголь разлагается и атомы углерода насыщают поверхности деталей. Ящик после цементации охлаждают на воздухе до температуры 300...400°С, извлекают из него детали, после чего про изводят термическую обработку деталей, как правило, закалку с последующим низким отпуском. Печь для твердой цементации 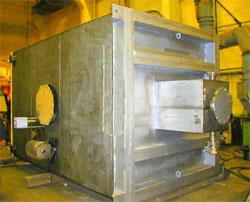 Газовая цементация осуществляется нагреванием изделий в среде углеродсодержащих газов (природный газ или пропан-бутановая смесь). Газовая цементация— более эффективный процесс, чем цементация в твердом карбюризаторе, так как отпадает необходимость в ящиках, которые следует нагревать, процесс легче автоматизируется и более экономичен. Кроме того, можно непосредственно из печи, где производится цементация, выполнять термообработку деталей. Время на цементацию и термообработку сокращается более чем в два раза. Цементации подвергаются стальные детали, работающие на истирание и испытывающие ударные нагрузки: валики, зубчатые колеса, поршневые пальцы, кулачки, пальцы звеньев гусениц и др. Т=920-930°С Выдержка 3-4 часа Охлаждение –воздух Печь для газовой цементации 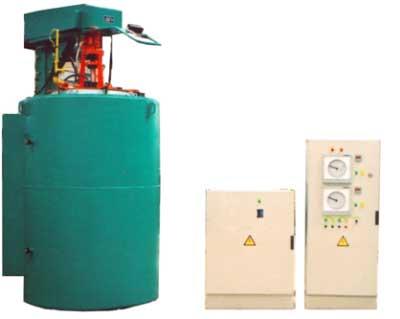 Жидкая цементация- она предназначена для мелких деталей(например болты, винты и т.д.) Жидкая цементация проводиться путём погружения детали в печь с раствором бензина(керосина)+BaCl2=CnHm. Т-840-860°С Время выдержки6часов Охлаждение-воздух Печь для жидкой цементации 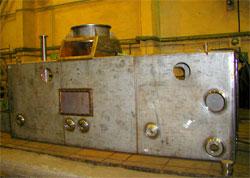 Азотирование (презентация) Азотирование–процесс химико-термической обработки, представляющий собой диффузионное насыщение поверхностного слоя стали азотом. Цель азотирования - получение поверхности деталей высокой твердости, износостойкости, высокой коррозионной стойкостью. Азотированию подвергаются детали, изготовленные из среднеуглеродистых легированных сталей марок 35ХМЮА и 38ХМЮА (цилиндров двигателя, насосы, зубчатых колес, валов, гильз и детали штампов шейки коленчатых валов, многие детали станков). Азотирование проводят по одноступенчатому режиму при нагреве детали до Т= 500...700°С в атмосфере аммиака выдержка 90 часов или по двухступенчатому режиму: Т = 500...520°С выдержкой 15-20 часов, Т = 550...570°С, выдержка 20-25 часов. Толщина слоя 0,3-0,6 мм. Твердость, азотированного слоя сохраняется при нагревании до температуры 600...650°С. Цианирование и нитроцементация(презентация) Поверхностное насыщение стали одновременно углеродом и азотом в расплавленной цианистой соли называется цианированием, а в газовой среде – нитроцементацией. Цель цианирования(нитроцементации)- получение высокой твердости и износостойкости поверхности деталей с сохранением пластичной сердцевины. Цианирование в зависимости от используемой среды цианирование проводят: в твердых средах; жидких средах; газовых средах.В зависимости от температуры нагрева цианирование подразделяется нанизкотемпературное и высокотемпературное.Цианирование в жидких средах производят с расплавленными солями в ваннах. Газовое цианирование производится в специально герметически закрытых печах. Высокотемпературное цианирование проводят при Т= 800…950 С. Выдержка от 1,5 до 6 часов. Толщина слоя от 0,5 до 2мм. После высокотемпературного цианирования детали подвергают закалке и низкому отпуску. Применяют в автомобильной и тракторной промышленности длямелких деталей из среднеуглеродистых сталей, работающих при небольших удельных нагрузках, а также для режущего инструмента из быстрорежущей стали.Для упрочнения валов, осей, зубчатых колёс и других деталей, работающих при значительных знакопеременных нагрузках. Основным недостатком цианирования является ядовитость цианистых солей. При нитроцементации изделия нагревают при Т=840—860°С в среде природного газа и аммиака. Выдержка в течении 8-10часов Толщинаслоя 0,25-1мм. Глубина слоя зависит от температуры и продолжительности выдержки. Посленитроцементации следует закалка, затем проводят отпуск при 160 – 180 ˚С.Нитроцементации подвергают детали сложной конфигурации, всевозможные шестерни склонные к короблению, шестерни привода масляного насоса в автомобилестроении, пальцы задних рессор, валики и т.д. Диффузионная металлизация (презентация) Диффузионная металлизация — насыщение поверхностного слоя деталей металлами (легирующими элементами) Цель диффузионной металлизации — повышение жаростойкости, коррозионной стойкости, износостойкости и твердости. Его осуществляют путём нагрева и выдержки стальных изделий в контакте с одним из перечисленных элементов, которые могут быть в твёрдом, жидком и газообразном состоянии. Процессы осуществляются при температуре 900...1150°С Более эффективно диффузионная металлизация проходит при использовании вместо порошкообразных смесей железа с легирующими элементами соответствующих хлористых соединений легирующих металлов (А1С1з, СгCl2, SiCl4 и т.д.), которые при высоких температурах диссоциируют, и поверхность изделий насыщается легирующими металлами. Продолжительность металлизации составляет 6... 12 ч. В зависимости от насыщающего элемента процесс диффузионной металлизации имеет определенное название, так, насыщение хромом — хромирование, алюминием — алитирование, кремнием - силицирование, бором — борирование и т. д.. Алитирование Алитирование - это процесс диффузионного насыщения поверхностного слоя стали алюминием. Алитирование проводят в средах:твердых и жидких. Цель: для повышения жаростойкости, окалиностойкости и коррозионной стойкости в атмосфере и морской воде. Алитирование в твердой среде при Т = 850 -900 С0 Время выдержки от 3-12часов Толщина слоя 0,3 – 0,5 мм Алитирование в твердой среде при Т = 750 -800 С0 Время выдержки от 45 – 90 минут Толщина слоя 0,20 – 0,35 мм Алитированию подвергают трубы, инструмент для литья цветных сплавов, чехлы термопар, детали газогенераторных машин и т.д Хромирование Хромирование - это процесс диффузионного насыщения поверхностного слоя стали хромом. Цель: получение высокой твердости, износостойкости, жаростойкости и коррозионной стойкости поверхности стальных изделий. Хромирование проходит в твердой, жидкой и газовой средах.Жидкостное хромирование проводят путем нагрева детали в ванне: Т = 900 -1100 С0 Время выдержки от 5-20часов Глубина слоя 0,1 – 0,3 мм.Хромирование применяют для пароводяной арматуры, клапанов, вентилей. Силицирование Силицирование–процесс химико-термической обработки, заключающийся в диффузионном насыщении поверхностного слоя стали кремнием. Цель- получение коррозионной стойкости и жаростойкости поверхности стальных деталей. Силицирование проводят в газовых средах при Т = 950—1100 °C, выдержка 2-5 часов, глубина слоя 0,6- 1,4 мм. Борирование Борирование- это процесс химико-термической обработки заключающийся в диффузионном насыщении поверхностного слоя стали бором. Цель: повышение износостойкости (в условиях сухого трения, скольжения со смазкой и без смазки, абразивного изнашивания), повышение коррозийной стойкости железоуглеродистых сплавов во многих агрессивных средах и жаростойкости при температурах ниже 850 С0 Борированию подвергают детали, применяемые в оборудовании нефтяной промышленности: втулки нефтяных насосов. Недостаток – слой обладает хрупкостью.Газовоеборирование проводят в специальных установках за счет разложения газообразных соединений бора. Газовое борирование проводят при Т=800-850°С. Время выдержки от 2 до 6 ч. Толщина слоя от 0,5 -1мм. 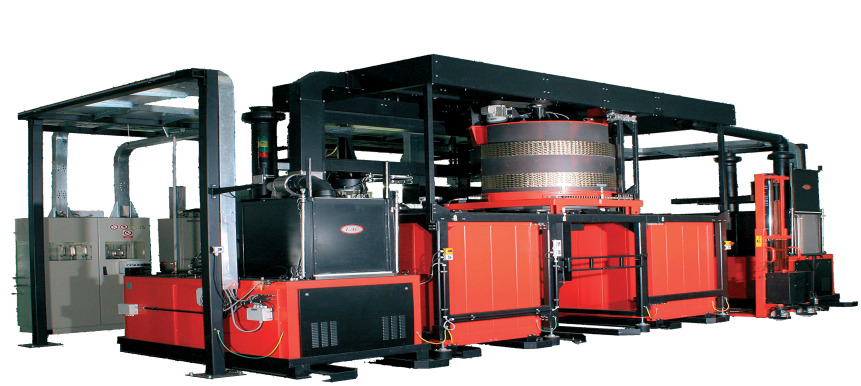 Автоматическая линия служит для термической и химико-термической обработки 1-В чём отличие химико-термической обработки от термической? 2-Какие химико-физические свойства обеспечиваются при химико-термической обработке? 3-Виды химико-термической обработки? 4-Что называется твёрдостью, износостойкостью, прочностью, вязкостью, пластичностью, упругостью? 5-Чем обусловлена высокая твёрдость цементационного слоя? 6-Напишите марки углеродистой стали для цементации? 7-Что называется карбюризатором? Обучающимся предлагается тест, который состоит из 10 вопросов Проверка: на экран выводится эталон ответов и критерии оценки, обучающиеся сами проверяют свои работы и выставляют себе оценки (Приложение 2) |