ВВЕДЕНИЕ
Способ газовой сварки был разработан в конце прошлого столетия, когда начиналось промышленное производство кислорода, водорода и ацетилена.
В тот период газовая сварка являлась основным способом сварки металлов и обеспечивала получение наиболее прочных сварных соединений. В дальнейшем с созданием и внедрением высококачественных электродов для дуговой сварки, автоматической и полуавтоматической дуговой сварки под флюсом и в среде защитных газов (аргона, гелия и углекислого газа и др.), газовая сварка была постепенно вытеснена из многих производств этими способами электрической сварки. Тем не менее, и до настоящего времени газовая сварка металлов наряду с другими способами сварки широко применяется в народном хозяйстве.
Сварку применяют для получения неразъемного соединения деталей при изготовлений изделий, машин и сооружений из металла. Прежде для этого преимущественно пользовались клепкой.
Сварное изделие имеет меньшей вес, чем клепальное, проще в изготовлении, дешевле, надежнее и может быть выполнено в более короткий срок, с меньшей затратой труда и материалов. Сваркой можно изготовлять изделия очень сложной формы, которые прежде удавалось получить только отливкой или кузнечной и механической обработкой. При изготовлении металлоконструкций сварка дает от 10 до 20 % экономии металла по сравнению с клепкой, до 30 % по сравнению с литьем из чугуна.
Сварные швы обеспечивают высокую надежность (плотность и прочность) резервуаров и сосудов, в том числе и работающих при высоких температурах и давлениях газов, паров и жидкостей.
Газовая сварка относится к сварке плавлением. Процесс газовой сварки состоит в нагревании кромок деталей вместе их соединения до расплавленного состояния пламенем сварочной горелки. Для нагревания и расплавления металла используется высокотемпературное пламя, получаемое при сжигании горючего газа в смеси с технически чистым кислородом. Зазор между кромками заполняется расплавленным металлом присадочной проволоки. Газовая сварка обладает следующими преимуществами: способ сварки сравнительно прост, не требует сложного и дорогого оборудования, а также источника электроэнергии. Изменяя тепловую мощность пламени и его положение относительно места сварки, сварщик может в широких пределах регулировать скорость нагрева и охлаждения свариваемого металла.
К недостаткам газовой сварки относятся меньшая скорость нагрева металла и большая зона теплового воздействия на металл, чем при дуговой сварке. При газовой сварке концентрация тепла меньше, а коробление свариваемых деталей больше, чем при дуговой сварке. Однако при правильно выбранной мощности пламени, умелом регулировании его состава, надлежащей марке присадочного металла и соответствующей квалификации сварщика газовая сварка обеспечивает получение высококачественных сварных соединений.
Благодаря сравнительно медленному нагреву металла пламенем и относительно невысокой концентрации тепла при нагреве производительность процесса газовой сварки существенно снижается с увеличением толщины свариваемого металла. Например, при толщине стали 1мм, скорость газовой сварки составляет около 10м/ч, а при толщине 10мм – только 2м/ч. Поэтому газовая сварка стали толщиной свыше 6мм менее производительна по сравнению с дуговой сваркой и применяется значительно реже.
Стоимость горючего газа (ацетилена) и кислорода при газовой сварке выше стоимости электроэнергии при дуговой и контактной сварке. Вследствие этого газовая сварка обходится дороже, чем электрическая.
Процесс газовой сварки труднее поддается механизации и автоматизации, чем процесс электрической сварки. Поэтому автоматическая газовая сварка многопламенными линейными горелками находит применении только при сварке обечаек и труб из тонкого металла продольными швами газовую сварку применяют при:
. изготовлении и ремонте изделий из тонко-листовой стали (сварке сосудов и резервуаров небольшой емкости, заварке трещин, сварке заплат и пр.);
. сварке трубопроводов малых и средних диаметров (до 100мм) фасонных частей к ним;
. ремонтной сварке литых изделий из чугуна, бронзы и силумина;
. сварке изделий из алюминия и его сплавов, меди, латуни, свинца;
. наплавке латуни на детали из стали и чугуна;
. сварке кованого и высокопрочного чугуна с применением присадочных прутков из латуни и бронзы, низкотемпературной сварке чугуна.
При помощи газовой сварки можно сваривать почти все металлы, применяемые в технике. Такие металлы, как чугун, медь, латунь, свинец легче поддаются газовой сварке, чем дуговой. Если учесть еще простоту оборудования то становится понятным широкое распространение газовой сварки в некоторых областях народного хозяйства (на некоторых заводах машиностроения, сельском хозяйстве, ремонтных, строительно-монтажных работах и др.).
аппаратура и оборудование для газовой резки
Баллоны для сжатых газов
Для хранения и транспортировки сжатых, сжиженных и растворенных газов, находящихся под давлением, применяют стальные баллоны. Баллоны имеют различную вместимость — от 0,4 до 55 дм3.
Баллоны представляют собой стальные цилиндрические сосуды, в горловине которых имеется конусное отверстие с резьбой, куда ввертывается запорный вентиль. Для каждого газа разработаны свои конструкции вентилей, что исключает установку кислородных вентилей на ацетиленовый баллон, и наоборот. На горловину плотно насаживается кольцо с наружной резьбой, служащее для навертывания предохранительного колпака, который служит для предохранения вентиля баллонов от возможных ударов при транспортировке.
Баллоны для сжатых, сжиженных и растворенных газов изготовляют согласно ГОСТ 949—73 из бесшовных труб углеродистой и легированной стали. Для сжиженных газов при рабочем давлении не свыше 30 кгс/см2 допускается применение сварных баллонов. Требования к баллонам регламентируются правилами Гостехнадзора СССР.
В зависимости от рода газа, находящегося в баллоне, баллоны окрашивают снаружи в условные цвета, а также соответствующей каждому газу краской наносят наименование газа. Например, кислородные баллоны окрашивают в голубой цвет, а надпись делают черной краской, ацетиленовый — в белый и красной краской, водородные — в темно-зеленый и красной краской, пропан — в красный и белой краской. Часть верхней сферической части баллона не окрашивают и выбивают на ней паспортные данные баллона: тип и заводской номер баллона, товарный знак завода-изготовителя, масса порожнего баллона, вместимость, рабочее и испытательное давление, дата изготовления, клеймо ОТК и клеймо инспекции Госгортехнадзора, дата следующего испытания. Баллоны периодически через каждые пять лет подвергают осмотру и испытанию.
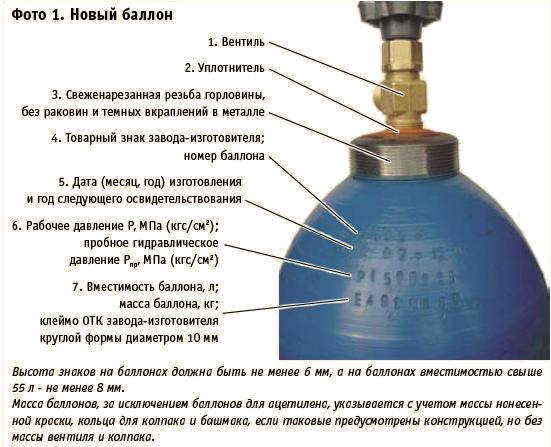
Вентили для баллонов
Вентили кислородных баллонов изготавливают из латуни. Сталь для деталей вентиля применять нельзя , так как она сильно коррозирует в среде сжатого влажного кислорода.
Ацетиленовые вентили изготавливают из стали. Запрещается применять медь и сплавы, содержащие свыше 70% меди, так как с медью ацетилен может образовывать взрывчатое соединение – ацетиленовую медь.
Редукторы для сжатых газов
При газовой сварке и резке металлов рабочее давление газов должно быть меньше, чем давление в баллоне или газопроводе. Для понижения давления газа применяют редукторы. Редуктором называется прибор, служащий для понижения давления газа, отбираемого из бал-, лона до рабочего и для автоматического поддержания этого давления постоянным, независимо от изменения давления газа в баллоне или газопроводе.
Согласно ГОСТ 6268-68 редукторы для газопламенной обработки классифицируются:
по принципу действия - на редукторы прямого и обратного действия;
по назначению и месту установки - баллонные (Б), рамповые (Р), сетевые (С);
по схемам редуцирования - одноступенчатые с механической установкой давления (О), двухступенчатые с механической установкой давления (Д), одноступенчатые с пневматической установкой давления (У);
по роду редуцируемого газа - ацетиленовые (А), кислородные (К), пропан-бутановые (П), метановые (М).
Редукторы отличаются друг от друга цветом окраски корпуса и присоединительными устройствами для крепления их к баллону. Редукторы, за исключением ацетиленовых, присоединяются накидными гайками, резьба которых соответствует резьбе штуцера вентиля. Ацетиленовые редукторы крепятся к баллонам хомутом с упорным винтом.
В практике наибольшее распространение получили редукторы обратного действия как более удобные и безопасные в эксплуатации.
Основные типы редукторов приведены в табл. 1.
Таблица №1. Основные типы редукторов
Редукторы |
Наименование газа | сетевые | баллонные | баллонные двухступенчатые | рамповые двухступенчатые | рамповые |
Кислород Ацетилен Водород Метан Пропан-бутан | ДКС-66 ДАС-66 - ДМС-66 ДПС-66 | ДКП-1-65 ДАП-1-65 ДВП-1-65 ДПП-1-65 | ДКД-8-65 ДАД-1-65 - - - | - ДАР-1-64 - - ДПР-1-64 | ДКР-250 ДКР-500 - - - |
Кислородные редукторы. Кислородные редукторы, применяемые при газовой сварке и резке металлов, окрашивают в голубой цвет и крепят к вентилям баллонов накидными гайками.
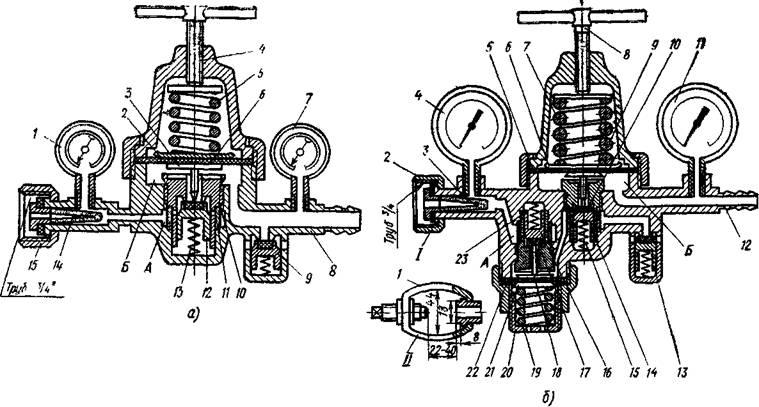
Рис. 1. Схемы кислородных редукторов: а - ДКП-1-65, б - ДКД
На рис. 1, а представлена схема баллонного кислородного одноступенчатого редуктора ДКП-1-65. Данному редуктору присвоен государственный Знак качества. Редуктор выпускается согласно ГОСТ 6268-68. Наибольшее допустимое давление газа на входе в редуктор-200 кгс/см2, наименьшее давление - 30 кгс/см2, наибольшее рабочее давление – 15 кгс/см2, наименьшее 1 кгс/см2. При наибольшем рабочем давлении расход газа составляет 60 м3/ч, при наименьшем - 7,5 м3/ч. Масса редуктора 2,3 кг.
Редуктор присоединяется к баллону накидной гайкой 15. Газ, пройдя фильтр 14, попадает в камеру высокого давления А. При вращении регулировочного винта 4 по часовой стрелке усилие нажимной пружины 5 передается через нажимной диск 2, мембрану "б и толкатель 3 на редуцирующий клапан 12, который, перемещаясь, открывает проход газу через образовавшийся зазор между клапаном 12 и седлом 10 в рабочую камеру Б. Регулирующий узел, состоящий из седла 10, клапана 12, пружины 13 и второго фильтра 11, выполнен в виде самостоятельного узла. На корпусе редуктора рабочей камеры Б установлен предохранительный клапан 9, отрегулированный на выпуск газа при давлении в рабочей камере Б в интервале 17,5-21,6 кгс/см2.
Давление в баллоне контролируется манометром 1, а в рабочей камере - манометром 7. Отбор газа осуществляется через ниппель 8, который присоединяется к редуктору гайкой с резьбой М16Х1,5. К ниппелю присоединяется шланг диаметром 9 мм, идущий к горелке или резаку.
Двухступенчатый кислородный редуктор ДКД изготовляется в двух вариантах: ДКД-8-65 для сварки и ДКД-15-65 для резки.
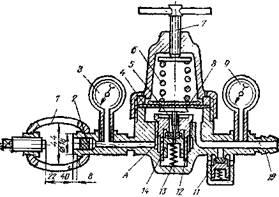
Рис. 2. Схема ацетиленового редуктора ДАП-1-65
Ацетиленовые редукторы. Ацетиленовый редуктор ДАП-1-65, предназначенный для понижения давления ацетилена , поступающего из баллона, рассчитан на наибольшее давление на входе-30 кгс/см2, наибольшее рабочее давление-1,2 кгс/см2, расход газа при наибольшем рабочем давлении-5 м3/ч. Наименьшее рабочее давление составляет 0,1 кгс/см2, расход газа при этом давлении - 3 м3/ч.
Редуктор присоединяется к вентилю баллона хомутом 1 (рис. 2).
Резаки для разделительной резки
Резак представляет собой горелку для кислородной резки металлов. Схема резака изображена на рис. 3, а. Он имеет рукоятку 9 и корпус 10, в который вставлена смесительная камера 14, присоединяемая к корпусу накидной гайкой 13. В смесительную камеру ввернуто сопло инжектора 12. Ацетилен поступает в резак по шланговому ниппелю 8, а кислород — по ниппелю 7.
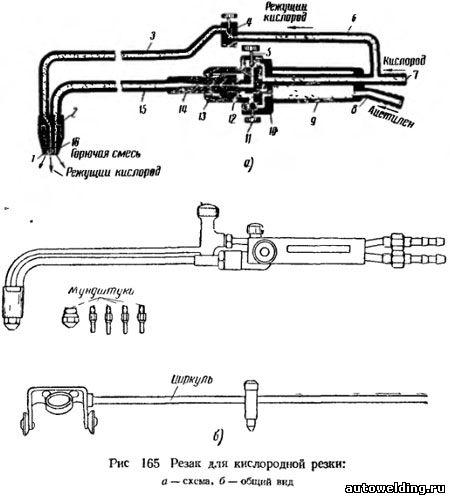
Рис. 3. резак для кислородной резки а – схема, б – общий вид
Кислород, поступающий через ниппель 7, идет по двум направлениям: часть его, используемая для подогревающего пламени и регулируемая вентилем 5, поступает в центральный канал инжектора 12, подсасывая ацетилен, количество которого регулируется вентилем 11. Из смесительной камеры горючая смесь по трубке 15 проходит в головку 2 резака, а затем, выходя через зазор между наружным мундштуком 16 и внутренним 1, сгорает, образуя подогревающее пламя.
Другая часть кислорода проходит по трубке 6 через вентиль 4 и далее по трубке 3 также поступает в головку 2 резака, откуда выходит через центральный канал внутреннего мундштука 1, образуя режущую струю кислорода.
Регулирование давления кислорода и подбор мундштуков в зависимости от толщины разрезаемого металла производится по данным табл. 2.
Таблица №2 Режимы резки резаком РР-53
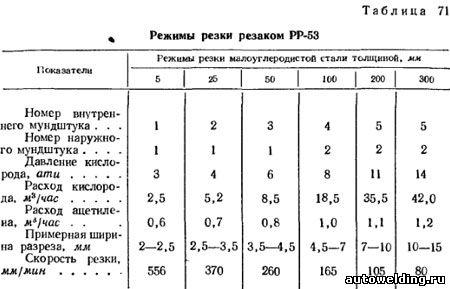
Давление ацетилена колеблется в пределах от 0,02 до 0,1 . Внешний вид резака РР-53 показан на рис.3, б.
Керосинорезы
В керосинорезах в качестве горючего используют керосин. Керосинорез К-51 (рис. 4) состоит из резака, бачка для жидкого горючего, шлангов, тележки и циркуля. Схема резака керосинореза изображена на рис. 5. Кислород через ниппель, вентиль 9 и инжектор 4 поступает в смесительную камеру головки 3. Здесь он смешивается с парами керосина или бензина, поступающими через второй ниппель и вентиль 7 в асбестовую набивку испарителя 11, в которой происходит испарение керосина под действием пламени вспомогательного мундштука 12. Горючая смесь выходит наружу через кольцевой зазор между мундштуками 1 и 2, образуя подогревающее пламя. Мощность и состав пламени регулируются вентилем 9 и маховичком 10, изменяющим положение инжектора в смесительной камере. Кислород проходит через вентиль 6 по трубке 5 в центральный канал мундштука 1. Для удобства работы резак снабжен рукояткой 8, в которой размещаются трубки для подвода керосина и кислорода.
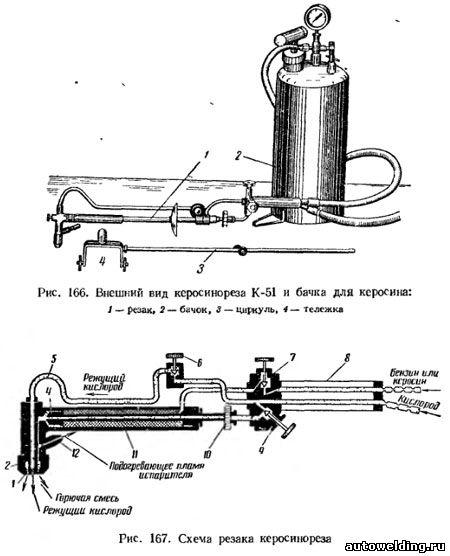
Рис. 4. Внешний вид керосинореза К-51 и бачка для керосина:
1 – резак, 2 – бачок, 3 – циркуль, 4 - тележка
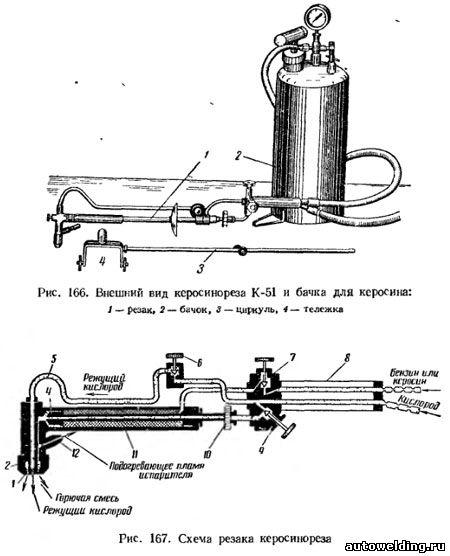
Рис. 5. Схема керосинореза
К
еросин должен подаваться в резак под давлением 0,5—2 ати. Для этого служит бачок емкостью 5 л, снабженный ручным воздушным насосом, манометром и запорным вентилем. Режимы резки керосинорезом приведены в табл. 3.
Таблица №3 Режимы резки керосинорезом
Для зажигания пламени керосина испаритель сначала нагревают паяльной лампой, горелкой или другим источником тепла. Предварительно в бачок насосом накачивают воздух до давления 2—2,5 атм., затем открывают вентиль подачи подогревающего кислорода и вентиль подачи горючего в резак, после чего регулируют подогревательное пламя, которое должно иметь правильную, слегка колоколообразную форму.
В настоящее время керосин используется также в горелках для сварки легкоплавких металлов, пайки и поверхностной закалки в качестве заменителя ацетилена. Принцип устройства и работы этих горелок такой же, как и у керосинореза, только в них отсутствуют вентили, трубки и каналы для режущего кислорода. В машинах для резки применяются керосинорезы с механическим распылением керосина струей кислорода и последующим испарением его в мундштуке головки.
Кислородная резка
Кислородная резка основана на сгорании металла в струе технически чистого кислорода. Металл при резке нагревают пламенем, которое образуется при сгорании какого-либо горючего газа в кислороде. Кислород, сжигающий нагретый металл, называют режущим. В процессе резки струю режущего кислорода подают к месту реза отдельно от кислорода, идущего на образование горючей смеси для подогрева металла. Процесс сгорания разрезаемого металла распространяется на всю толщину, образующиеся окислы выдуваются из места реза струёй режущего кислорода.
Металл, подвергаемый резке кислородом, должен удовлетворять следующим требованиям: температура воспламенения металла в кислороде должна быть ниже температуры его плавления; окислы металла должны иметь температуру плавления ниже, чем температура плавления самого металла, и обладать хорошей жидкотекучестью; металл не должен иметь высокой теплопроводности. Хорошо поддаются резке низкоуглеродистые стали.
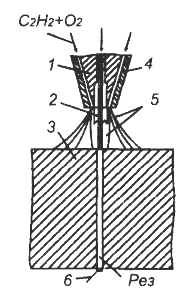
Рис. 6 Схема процесса газокислородной резки:
- режущий мундштук; 2- режущий кислород; 3- разрезаемый металл; 4 – подогревательный мундштук; 5 - подогревательное пламя; 6 - шлаки
Для кислородной резки пригодны горючие газы и пары горючих жидкостей, дающие температуру пламени при сгорании в смеси с кислородом не менее 1800 гр. Цельсия. Особенно важную роль при резке имеет чистота кислорода. Для резки необходимо применять кислород с чистотой 98,5 - 99,5 %. С понижением чистоты кислорода очень сильно снижается производительность резки и увеличивается расход кислорода. Так при снижении чистоты с 99,5 до 97,5 % (т.е. на 2 %) - производительность снижается на 31 %, а расход кислорода увеличивается на 68,1 %.
Резка может осуществляться вручную или машинным способом, выполняемым на полуавтоматах и автоматах. Схема процесса разделительной газокислородной резки представлена на рис. 6 Смесь кислорода с горючим газом выходит из подогревательного мундштука резака и сгорает, образуя подогревательное пламя. Этим пламенем металл нагревается до температуры начала его горения. После этого по осевому каналу режущего мундштука подается струя режущего кислорода. Кислород попадает на нагретый металл и зажигает его. При его горении выделяется значительное количество теплоты, которое совместно с теплотой, выделяемой подогревательным пламенем, передается нижележащим слоям металла, которые также сгорают. Образующиеся при этом шлаки (оксиды железа и т.д.) выдуваются струей режущего кислорода из зазора между кромками реза. Для проведения кислородной резки металл должен удовлетворять следующим требованиям:
Температура горения металла должна быть ниже температуры его плавления, т.е. металл должен гореть в твердом состоянии. В противном случае расплавленный металл трудно удалять из полости реза.
Температура плавления образующихся при резке оксидов должна быть ниже температуры плавления самого металла. В этом случае оксиды легко выдуваются из полости реза.
Тепловой эффект образования оксидов должен быть высоким.
При резке стали основное количество теплоты (70 ... 95 %) образуется при окислении металла. Этим условиям удовлетворяют низкоуглеродистые и низколегированные стали, титановые сплавы. Чугун не режется кислородом вследствие низкой температуры плавления и высокой температуры горения; медь - из-за высокой температуры плавления и малой теплоты сгорания; алюминий - из-за высокой тугоплавкости образующихся оксидов. Высоколегированные стали (хромистые, хромоникелевые и т.д.) не режутся ввиду образования тугоплавких, вязких шлаков.
Поверхность разрезаемого металла должна быть очищена от ржавчины и других загрязнений. Металл устанавливается в положение, лучше всего в нижнее, но так, чтобы был свободный выход режущей струи с обратной стороны. Операция резки начинается с предварительного подогрева в месте реза при температуре горения металла (1200 ... 1350 °С). Устанавливаемая мощность подогревающего пламени зависит от рода горючего газа, толщины и состава разрезаемого металла.
Начинают резку обычно с кромки металла. При толщинах до 80 ... 100 мм можно прорезать отверстие в любом месте листа. Ядро подогревающего пламени находится на расстоянии 2 ... 3 мм от поверхности металла. Когда температура подогреваемого металла достигнет необходимой величины, пускают струю режущего кислорода. Чем выше чистота режущего кислорода, тем выше качество и производительность резки. По мере углубления режущей струи в толщу реза уменьшается скорость и мощность струи режущего кислорода. Поэтому наблюдается ее искривление (рис. 7), для уменьшения которого дается наклон режущей струи. При резке толстого металла ширина реза увеличивается к нижней кромке из-за расширения струи режущего кислорода. На кромках с их нижней стороны остается некоторое количество шлака.
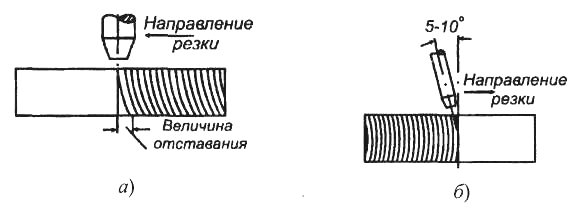
Рис. 7. Отставание режущей струи (а); резак, наклоненный для уменьшения отставания струи (б)
В металле, на поверхности реза, повышается содержание углерода. Причина этого в том, что при горении углерода образуется окись углерода СО, при взаимодействии которой с железом в нем и повышается содержание углерода. Возможна и диффузия углерода к кромке реза из близрасположенных участков металла.
Если производится последующая сварка для предупреждения повышения углерода в металле шва (образование закаленных структур), следует производить механическую обработку или зачистку поверхности реза. В процессе реза происходит термообработка металла кромок реза, соответствующая закалке. Ширина зоны термического влияния (до 6 мм) зависит от химического состава и возрастает с увеличением толщины разрезаемого металла.
Низкоуглеродистая сталь закалке практически не поддается. Происходит только укрупнение зерна и появление в структуре наряду с перлитом участков сорбита. При резке сталей с повышенным содержанием углерода или легирующих примесей в структуре металла может появиться троостит и даже мартенсит. Неравномерный нагрев кромок создает напряжения в металле и деформирует его. Кромки реза несколько укорачиваются, а в прилегающем слое возникают растягивающие напряжения, которые могут привести к образованию трещин.
Своеобразным способом является резка кислородным копьем (прожигание отверстий). Для этого используются длинные толстостенные трубки диаметром 8 ... 10 мм из низкоуглеродистой стали. До начала резки рабочий конец трубки нагревают сварочным пламенем или угольной электрической дугой до температуры воспламенения металла в кислороде. При включении режущего кислорода конец трубки воспламеняется. Затем рабочий конец трубки слегка прижимают к металлу и углубляют в него, выжигая отверстие. Образующийся шлак выдувается из отверстия наружу избыточным кислородом и образующимися газами. При значительной глубине прожигаемого отверстия изделие нужно ставить в положение, облегчающее вытекание шлаков.
Многие легированные стали плохо поддаются обычной кислородной резке. Например, все стали со значительным содержанием хрома (при резке образуется тугоплавкий окисел хрома), чугун, цветные металлы. Однако они поддаются кислородно-флюсовой резке. При этом способе в зону резки режущим кислородом вдувается порошкообразный флюс. Он состоит, главным образом, из порошка металлического железа. Сгорая в струе кислорода, порошок дает дополнительное количество тепла, а образующиеся оксиды, смешиваясь с оксидами разрезаемого металла, разжижают их. В зависимости от состава разрезаемого металла во флюс могут добавляться и другие добавки, например, кварцевый песок, порошок алюминия и др.
Газовая резка с водородно-кислородным или бензинокислородным подогревающим пламенем применяется при работах под водой. При электрокислородной резке используются стальные или графитовые трубки, через которые подается режущий кислород. Подогрев металла осуществляется сварочной дугой.
Параметры режимов резки низкоуглеродистой стали приведены в таблице:4
Толщина мм | Сопло | Гильза | Камера | Давление Мпа | Скорость мм/мин | Расход, м3/час | Расход2, м3/час | Ширина, мм | Расстояние, мм |
1 | 2 | 3 | 4 | 5 | 6 | 7 | 8 | 9 | 10 |
5 | 0-1 | 3П | 1ПБ | 0,3 | 650 | 2,5 | 0,5 | 3 | 4 |
10 | 2 | | 0,4 | 550 | 3,75 | 0,52 | 3,3 | 5 |
20 | | 0,45 | 475 | 5,25 | 0,55 | 3,5 |
30 | 3 | | 0,5 | 380 | 7 | 0,58 | 4 | 6 |
40 | | 0,55 | 340 | 8 | 0,6 | 5 |
50 | | 0,6 | 320 | 9 | 0,65 |
60 | 5П | 0,65 | 300 | 10 | 0,7 |
80 | 4 | 0,7 | 275 | 12 | 0,75 |
100 | 0,75 | 225 | 14 | 0,85 | 5,5 | 8 |
160 | 5 | 0,8 | 170 | 18 | 0,95 | 6 | 10 |
200 | 6 | 0,85 | 150 | 22 | 1,1 | 7,5 | 12 |
300 | 6П | 0,9 | 90 | 25 | 1,2 | 9 |
Таблица №5 Режимы ручной газовой резки с применением в качестве горючего газа ацетилена.
Толщина металла, мм | Номер внутреннего мундштука | Давление на входе в горелку, МПа (кгс/см2) | Время нагрева при пробивании отверстия кислородной струей, сек. | Ширина реза, мм | Расход газов, м3/ м пог. реза |
ацетилен | кислород | ацетилен | кислород |
4 | 1 | 0,04 (0,40) | 0,25 (2,50) | 5-8 | 2,0 | 0,059 | 0,285 |
6 | 1 | 0,04 (0,40) | 0,30 (3,00) | 5-8 | 2,5 | 0,063 | 0,330 |
8 | 1 | 0,04 (0,40) | 0,30 (3,00) | 5-8 | 2,5 | 0,067 | 0,370 |
10 | 1 | 0,05 (0,50) | 0,35 (3,50) | 8-10 | 2,5 | 0,070 | 0,410 |
12 | 1 | 0,05 (0,50) | 0,35 (3,50) | 8-10 | 3,0 | 0,073 | 0,450 |
13 | 1 | 0,05 (0,50) | 0,35 (3,50) | 8-10 | 3,0 | 0,075 | 0,470 |
15 | 1 | 0,05 (0,50) | 0,35 (3,50) | 8-10 | 3,0 | 0,079 | 0,515 |
18 | 2 | 0,05 (0,50) | 0,40 (4,00) | 10-13 | 3,0 | 0,084 | 0,575 |
20 | 2 | 0,05 (0,50) | 0,40 (4,00) | 10-13 | 3,0 | 0,087 | 0,615 |
25 | 3 | 0,06 (0,60) | 0,45 (4,50) | 13-15 | 3,5 | 0,095 | 0,715 |
30 | 3 | 0,06 (0,60) | 0,50 (5,00) | 13-15 | 3,5 | 0,103 | 0,820 |
36 | 3 | 0,06 (0,60) | 0,50 (5,00) | 15-20 | 3,5 | 0,114 | 0,945 |
40 | 3 | 0,07 (0,70) | 0,50 (5,00) | 15-20 | 4,0 | 0,121 | 1,025 |
50 | 3 | 0,07 (0,70) | 0,60 (6,00) | 18-25 | 4,0 | 0,132 | 1,235 |
60 | 4 | 0,07 (0,70) | 0,65 (6,50) | 20-28 | 4,5 | 0,148 | 1,445 |
Таблица №6 Режимы ручной газовой резки с применением в качестве горючего газа пропан-бутана.
Толщина металла, мм | Номер внутреннего мундштука | Давление на входе в горелку, МПа (кгс/см2) | Время нагрева при пробивании отверстия кислородной струей, сек. | Ширина реза, мм | Расход газов, м3/ м пог. реза |
пропан-бутан | кислород | пропан-бутан | кислород |
4 | 1 | 0,04 (0,40) | 0,30 (3,00) | 5-8 | 2,5 | 0,035 | 0,289 |
6 | 1 | 0,04 (0,40) | 0,30 (3,00) | 6-10 | 3,0 | 0,037 | 0,334 |
8 | 1 | 0,04 (0,40) | 0,35 (3,50) | 6-10 | 3,0 | 0,039 | 0,375 |
10 | 2 | 0,05 (0,50) | 0,35 (3,50) | 8-13 | 3,0 | 0,041 | 0,415 |
12 | 2 | 0,05 (0,50) | 0,40 (4,00) | 8-13 | 3,5 | 0,043 | 0,465 |
13 | 2 | 0,05 (0,50) | 0,40 (4,00) | 10-15 | 3,5 | 0,044 | 0,476 |
15 | 2 | 0,05 (0,50) | 0,40 (4,00) | 10-15 | 3,5 | 0,046 | 0,522 |
18 | 2 | 0,05 (0,50) | 0,40 (4,00) | 10-15 | 3,5 | 0,049 | 0,582 |
20 | 2 | 0,06 (0,60) | 0,45 (4,50) | 13-18 | 4,0 | 0,051 | 0,623 |
25 | 3 | 0,06 (0,60) | 0,50 (5,00) | 15-20 | 4,0 | 0,056 | 0,724 |
30 | 3 | 0,06 (0,60) | 0,55 (5,50) | 18-23 | 4,0 | 0,061 | 0,830 |
36 | 3 | 0,07 (0,70) | 0,55 (5,50) | 20-25 | 4,5 | 0,066 | 0,956 |
40 | 4 | 0,07 (0,70) | 0,60 (6,00) | 22-28 | 4,5 | 0,071 | 1,037 |
50 | 4 | 0,07 (0,70) | 0,65 (6,50) | 25-30 | 5,0 | 0,078 | 1,249 |
60 | 4 | 0,08 (0,80) | 0,70 (7,00) | 25-30 | 5,0 | 0,087 | 1,461 |
Таблица №7 Режимы ручной газовой резки с применением в качестве горючего газа - природного газа.
Толщина металла, мм | Номер внутреннего мундштука | Давление на входе в горелку, МПа (кгс/см2) | Время нагрева при пробивании отверстия кислородной струей, сек. | Ширина реза, мм | Расход газов, м3/ м пог. реза |
природный газ | кислород | природный газ | кислород |
4 | 1 | 0,05 (0,50) | 0,30 (3,00) | 6-10 | 3,0 | 0,107 | 0,353 |
6 | 1 | 0,05 (0,50) | 0,30 (3,00) | 6-10 | 3,0 | 0,113 | 0,306 |
8 | 1 | 0,05 (0,50) | 0,30 (3,00) | 6-10 | 3,5 | 0,119 | 0,443 |
10 | 1 | 0,05 (0,50) | 0,35 (3,50) | 8-13 | 3,5 | 0,125 | 0,492 |
12 | 1 | 0,06 (0,60) | 0,35 (3,50) | 10-15 | 3,5 | 0,131 | 0,532 |
13 | 1 | 0,06 (0,60) | 0,35 (3,50) | 10-15 | 3,5 | 0,134 | 0,554 |
15 | 2 | 0,06 (0,60) | 0,35 (3,50) | 12-17 | 4,0 | 0,140 | 0,597 |
18 | 2 | 0,06 (0,60) | 0,40 (4,00) | 13-18 | 4,0 | 0,149 | 0,667 |
20 | 2 | 0,06 (0,60) | 0,40 (4,00) | 15-20 | 4,0 | 0,155 | 0,708 |
25 | 2 | 0,07 (0,70) | 0,40 (4,00) | 18-22 | 4,0 | 0,170 | 0,823 |
30 | 3 | 0,07 (0,70) | 0,45 (4,50) | 20-25 | 4,0 | 0,185 | 0,933 |
36 | 3 | 0,07 (0,70) | 0,45 (4,50) | 22-28 | 4,5 | 0,203 | 1,061 |
40 | 3 | 0,08 (0,80) | 0,50 (5,00) | 25-30 | 4,5 | 0,215 | 1,146 |
50 | 4 | 0,08 (0,80) | 0,55 (5,50) | 27-35 | 5,0 | 0,235 | 1,361 |
60 | 4 | 0,08 (0,80) | 0,60 (6,00) | 30-35 | 5,0 | 0,264 | 1,577 |
Таблица №8 Классификация сталей по разрезаемости их кислородной резкой и технологические особенности процесса резки.
Группа стали | Сэ | Марка стали | Технологические особенности процесса резки |
1 | До 0,54 | Стали углеродистые обыкновенного качества марок Ст1-Ст5 по ГОСТ 380-88 | Резка без технологических ограничений |
Стали углеродистые качественные марок 05-30 по ГОСТ 1050-88 |
0,40-0,54 | Стали низколегированные марок 09Г2С; 14Г2; 09Г2СД; 15ГФ и др. по ГОСТ 19282-73 |
Стали легированные марок 15Х; 20Х; 15Г; 15ХМ; 12ХН2 и др. по ГОСТ 4543-71 |
2 | 0,54-0,70 | Углеродистые стали Ст6; Сталь 35-50 по ГОСТ 1050-88, ГОСТ 380-88 | Предварительный или сопутствующий подогрев до 150 С, охлаждение на воздухе. Возможна резка без подогрева на пониженной скорости с последующим отжигом или отпуском. |
Легированные стали марок 30Х; 35Х; 18ХГ; 25ХГТ; 25ХГМ и др. по ГОСТ 4543-71 |
3 | 0,70-0,94 | Сталь 55; 60; 38ХА; 40Х-50Х; 35Г2; 45ХН; 38Х2Ю; 35ХГСА | Предварительный подогрев до 250-350 С, последующее медленное охлаждение под асбестовым полотном или в песке. |
4 | 0,94 | 35ХС; 38ХС; 40ХС; 50ХГСА; 50ХГФА; 12Х2Н3МА и др. | Предварительный подогрев 350 С, последующим охлаждением в печи. |
Технология сварки низколегированных сталей
Низколегированные низкоуглеродистые стали 0,9Г2; 0,9Г2С; 10ХСНД; 10Г2С1; 10Г2С при сварке покрытыми электродами не закаливаются и мало склонны к перегреву. Сварку этих сталей производят аналогично сварке низкоуглеродистой стали.
Для обеспечения равнопрочности соединения ручную сварку выполняют электродами типа Э50А. Твердость и прочность околошовной зоны практически не отличается от основного металла.
Низколегированные низкоуглеродистые стали 12ГС; 14Г; 14Г2; 14ХГС; 15ХСНД; 15К2Ф; 15Г2СФ; 15Г2АФ при сварке могут образовывать закалочные микроструктуры и перегрев металла шва в зоне термического влияния. Количество закаливающихся структур резко уменьшается, если сварка выполняется с относительной погонной энергией, которая необходима для уменьшения скорости охлаждения сварного соединения. Однако снижение скорости охлаждения металла при сварке приводит к укрупнению зерен (перегреву) металла шва и околошовного металла из-за повышенного содержания углерода в этих сталях. Это особенно касается сталей 15СНД; 14ХС. Стали 15Г2Ф; 15Г2ФС; 15Г2АФ менее склоны к перегреву в околошовной зоне, так как они легированы ванадием и азотом. Поэтому сварка большинства указанных сталей ограничивается более узкими пределами тепловых режимов, чем сварка низкоуглеродистой стали.
Режим сварки необходимо подбирать так, чтобы не было большого количества закалочных микроструктур и сильного перегрева металла. Тогда можно производить сварку стали любой толщины без ограничения при окружающей температуре не ниже -100 С. При более низкой температуре необходим предварительный подогрев до 120-1500С. При температуре ниже -250С сварка изделий из закаливающихся сталей запрещается.
Для предупреждения большого перегрева сварку стали 15ХСНД и 14ХС следует проводить на пониженной погонной тепловой энергии (при пониженных значениях токах электродами меньшего диаметра) по сравнению со сваркой низкоуглеродистой стали.
Для обеспечения равнопрочности основного металла и сварного соединения при сварке этих сталей надо применять электроды типа Э50А или Э55А.
Технология сварки низколегированных среднеуглеродистых сталей 17ГС; 18Г2АФ; 35ХМ и других подобных технологии сварки среднелегированных сталей.
При газовой сварке низколегированных сталей 10ХСНД и 15ХСНД применяют нормальное пламя. Они хорошо свариваются газовой сваркой. Мощность сварочного пламени выбирается из расчета расхода ацетилена 75-100 дм3 / ч при левом способе и 100-130 дм3 / ч при правом способе на 1 мм толщины свариваемого металла. В качестве присадки используется сварочная проволока Св-08; Св-08А; Св-10Г2. Сварка осуществляется без применения флюса. Для повышения механических свойств металла шов проковывают при светло-красном калении (800-8500С) с последующей нормализацией.
Низколегированные теплоустойчивые молибденовые стали (12М; 15М; 20М; 25МЛ) и хромомолибденовые (10ХМ; 15ХМ; 20ХМ; 30ХМ) стали – сварку этих сталей выполняют нормальным ацетилено-кислородным пламенем. Мощность сварочного пламени выбирают из расчета расхода ацетилена 100 дм3 / ч на 1 мм толщины свариваемого металла. В качестве присадочной проволоки используют проволоки марок Св-08ХНМ; Св-10ХНМА; Св-18ХМА; Св-08ХМ; Св-10ХМ. Сварку этих сталей ведут обратноступенчатым способом небольшими участками длиной 16-25 мм. В связи с тем, что эти стали способны к закалке на воздухе, рекомендуется сваривать их с предварительным подогревом до 250-3000С. При сварке применяют как левый, так и правый способы сварки. Кромки свариваемого металла перед сваркой зачищают до металлического блеска. При толщине металла до 5 мм сварку проводят за один проход, при большей толщине применяют многослойную сварку. Сварку рекомендуется вести с наименьшем числом перерывов. При возобновлении сварки после перерыва необходимо подогреть весь стык до 250-3000С. После окончания сварки пламя горелки медленно отводят вверх. Это способствует более полному выделению газов из расплавленного металла. При сварке необходимо следить за тем, чтобы переход от усиления шва к основному металлу был плавным по всей длине шва. Хромомолибденовые стали свариваются хуже, чем молибденовые. Это обуславливается наличием Сr, который образует тугоплавкие оксиды. Сварные изделия из хромомолибденовой и молибденовой стали после сварки подвергают термообработке. Сварные изделия из молибденовой стали нагревают горелкой до 9000С, изделия из хромомолибденовой стали – до 930-9500С. Ширина нагрева должна в 5 раз превышать ширину шва. После нагрева до указанных температур изделия охлаждают на воздухе. Указанные мероприятия обеспечивают получение сварного соединения, близкого по прочности к основному металл.
Легированными называют такие стали, в состав которых входят легирующие элементы, отсутствующие в углеродистой стали, или те же кремний и марганец, но в повышенном по сравнению с углеродистой сталью количестве.
Легирующие элементы в такой стали взаимодействуют с железом и углеродом и тем самым изменяют механические и физико-химические свойства металла. Как правило, легированные стали характеризуются высокими механическими свойствами, рядом специальных свойств (жаростойкость, коррозионная стойкость и др.) и повышенной стойкостью против хрупкого разрушения. Отмеченные особенности этих сталей широко используют при изготовлении из них соответствующих конструкций.
Легированные стали часто разделяют на три группы низко-, средне- и высоколегированные. В зависимости же от микроструктуры, получаемой при охлаждении на спокойном воздухе стандартных образцов, нагретых выше А3, эти стали разбивают на четыре структурных класса: 1) перлитный; 2) мартенситный; 3) ферритный; 4) аустенитный. Низколегированные стали относятся к перлитному классу, среднелегированные — к перлитному или мартенситному, высоколегированные стали — к мартенситному и последующим двум классам. Для свариваемости каждой из названных групп сталей характерны свои особенности.
К низколегированным относят такие стали, которые легированы одним или несколькими элементами при содержании каждого из них ≤2% и суммарном содержании легирующих элементов ≤5%. Эти стали делят на три группы: низкоуглеродистые конструкционные; жаропрочные; среднеуглеродистые конструкционные.
Низкоуглеродистые низколегированные конструкционные стали можно в свою очередь разделить на стали повышенной прочности и высокопрочные.В сталях повышенной прочности (НЛ1, НЛ2, 10Г2СД, 14ХГС, 10ХСНД, 12ХГН, 09Г2ДТ и др.) содержание углерода не превышает 0,23%. Эти стали используют в машиностроении и строительстве. Поставляют их преимущественно в горячекатаном виде.
Легирующие элементы — Mn, Si, Ni, Cr, Сu, Ti — растворяются в феррите, упрочняют его и измельчают перлит. Благодаря этому прочностные характеристики таких сталей повышаются и предел прочности доходит до 55 кГ/мм2.
Технология сварки низколегированных сталей в смесях инертных газов
Широко распространенная сварка в двуокиси углерода, обладая неоспоримыми преимуществами перед ручной дуговой сваркой, имеет ряд существенных недостатков, которые практически перечеркивают на нет, при сварке ответственных металлоконструкций, все ее преимущества. Сварке в двуокиси углерода присуще увеличенное разбрызгивание, требующее значительных трудовых затрат на зачистку сварного соединения и околошовной зоны, сварные соединения обладают малой энергоемкостью разрушения.
Предлагаемая технология механизированной сварки в смеси аргона с двуокисью углерода позволяет значительно улучшить, в сравнении со сваркой в СО2 технологические параметры процесса сварки.
Существенно повышаются механические характеристики сварного соединения, особенно при отрицательных температурах. Так при температуре 20°С KCV=46 и 65 Дж/см соответственно для сварки в СО2 и Аг+СО2, а при температуре -40°С KCV=25 и 53 Дж/см , при этом первая критическая температура хрупкости, которая равна минус 10°С для сварки в СО2 снижается до минус 20°С для сварки в смеси.
Потери электродного металла, достигающие при сварке в СО2 100...140 кг на тонну наплавленного металла, могут быть снижены до 20...30 кг при сварке в смеси Аг+СО2. При этом достигается существенная экономия трудозатрат и времени на очистку деталей сварочного оборудования, шва и зоны, прилегающей к нему от брызг электродного металла.
Таблица №9 Технологические параметры сварки низколегированных сталей в среде защитных газов
Технологический параметр | Диаметр сварочной проволоки, мм |
1,2 | 1,6 |
Сила сварочного тока, А |
170 | 250 | 290 | 340 |
Защитная атмосфера |
СО2 | Аг+СО2 | СО2 | Аг+СО2 | СО2 | Аг+СО2 | СО2 | Аг+СО2 |
Разбрызгивание на деталь, г/час | 215 | 60 | 320 | 25 | 285 | 70 | 105 | 10 |
Разбрызгивание на сопло, г/час | 80 | 20 | 195 | 20 | 120 | 80 | 100 | 5 |
Площадь проплавления, мм2 | 8 | 9 | 21 | 18 | 24 | 16 | 34 | 30 |
Глубина проплавления, мм | 1,8 | 1,7 | 3,4 | 3,8 | 3,8 | 3,8 | 4,9 | 5,7 |
Ширина шва, мм | 5,8 | 7,3 | 9,8 | 11,5 | 10,8 | 12,1 | 11 | 12,2 |
Высота выпуклости, мм | 2,6 | 2,7 | 2,2 | 2,2 | 1,9 | 1,7 | 2,8 | 2,5 |
Свариваемость низколегированных сталей
По своей свариваемости стали этой группы мало отличаются от нелегированных низкоуглеродистых. Однако они более склонны к росту зерна в околошовной зоне, а при высоких скоростях охлаждения в ней могут появиться неравновесные структуры закалочного характера.
Низкоуглеродистые высокопрочные стали (14Х2ГМР, 14ХМНДФР, 16Г2АФ, 12ХГ2СМФ и др.) относят к термически упрочняемым сталям, для которых наряду с высокой прочностью (σв ≥ 80 кГ/мм2) характерны достаточная пластичность, вязкость, повышенное сопротивление хрупким разрушениям, коррозионная стойкость и др. Применение таких сталей в машиностроении и строительстве позволяет значительно снизить вес конструкций и повысить их несущую способность. Упрочнения этих сталей достигают сочетанием минимального легирования с термической обработкой — обычно закалкой и отпуском. Таким образом создается весьма измельченная структура с мелкодисперсными упрочняющими частицами карбидов или нитридов.
Однако свариваемость высокопрочных сталей хуже свариваемости низкоуглеродистых низколегированных, так как:
1) в околошовной зоне сварных соединений возможно образование холодных трещин;
2) в зоне термического влияния вероятно появление участка разупрочнения, снижающего прочность сварного соединения.
Вследствие наличия легирующих элементов, повышающих устойчивость аустенита, эти стали чувствительны к скорости охлаждения. Но опасность возникновения холодных трещин в околошовной зоне здесь меньшая, чем в углеродистых конструкционных сталях, так как мартенситное (или бейнитное) превращение из-за низкого содержания углерода протекает при относительно высоких температурах ( 350 °С) и сопровождается сравнительно низкими напряжениями второго рода (микронапряжениями). К тому же малоуглеродистый игольчатый мартенсит, или бейнит-структура, более пластичен. Все же. поскольку эти структуры обладают пониженной проницаемостью для водорода, диффундирующий из шва водород скапливается на границах зерен, имеющих неупорядоченное строение с большей концентрацией дефектов и искажений, и создает дополнительные микронапряжения, способствующие появлению холодных трещин. Уменьшение скорости охлаждения в околошовной зоне, как и средства по снижению количества растворенного в металле сварочной ванны водорода, позволяют получить стойкий в отношении холодных трещин металл.
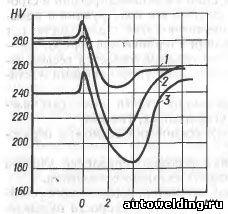
Рис 8. Кривые распределения по длине зоны l твердости в сварном соединении из термоупрочненных сталей.
Разупрочнение в зоне термического влияния, сопровождаемое провалом твердости (рис. 8), может достигать 30% и более. Его появление связано с действием сварочного нагрева и касается тех участков зоны, максимальная температура нагрева которых лежит в пределах 500 °С — Асз (участки рекристаллизации и неполной перекристаллизации). Чаще всего разупрочнение связано с двумя процессами: 1) распадом пересыщенного твердого раствора и обеднением его упрочняющими легирующими элементами; 2) образованием карбидных фаз и коагуляцией их. Степень разупрочнения зависит от химического состава стали и ее термической обработки и увеличивается с повышением погонной энергии сварки: на рис. 190 кривая 1 представлена для стали 14ХМНДФР (qп — 8000 кал/см); кривая 2 — для 15ХСНД (qп — 7500 кал/см), а кривая 3 — для стали 15ХНД (qп — 12 ООО кал/см).
Значительно уменьшить и даже устранить разупрочнение можно, увеличив скорость охлаждения при сварке. Однако в этом случае следует учитывать возможность появления закалочных структур в околошовной зоне. Поэтому регулировать термический цикл при сварке термоупрочняемых сталей следует весьма продуманно.
Жаропрочные низколегированные
Стали (15М, 15ХМА, 20ХМА, 20ХМФЛ и др.) обладают повышенной технической прочностью при высоких температурах и длительных постоянных нагрузках. Их жаропрочность оценивается величиной предела ползучести (Ползучесть—это способность нагретого до высокой температуры металла постепенно пластически деформироваться под воздействием длительной постоянной нагрузки. Отсюда предел ползучести— напряжение, при котором через определенный промежуток времени при заданной температуре деформация ползучести получит заранее установленную величину) и предела длительной прочности (Пределом длительной прочности называется минимальное напряжение, вызывающее разрушение металла при заданной температуре за определенный отрезок времени (1000 ч, 10 000 ч и т. д.)). Применяют эти стали для изготовления конструкций, работающих в условиях высоких температур (350— 450 °С) и значительных напряжений, а также в средах, способствующих химическому и механическому разрушению металла (паровые котлы, нефтеаппаратура и пр.).Обычно в такие стали для повышения их жаропрочности вводят специальные легирующие элементы (Mo, V, W). которые повышают температуру разупрочнения металла при нагреве и стойкость металла к разупрочнению. Для одновременного повышения жаростойкости стали в ее состав вводят Сr, создающий защитную пленку оксидов на поверхности металла (жаростойкость — устойчивость против окисления при высоких температурах). Применяют жаропрочные стали, как правило, после термообработки (нормализация с отпуском, закалка с отпуском и др.).
Стали этой группы обладают удовлетворительной свариваемостью. Однако при этом нужно обязательно получать металл шва, близкий по составу к основному, чтобы предупреждать развитие диффузионных процессов в условиях высоких температур. Тем самым достигается и необходимая равнопрочность металла шва с основным металлом.
Жаропрочные низколегированные стали характеризуются повышенной чувствительностью к закалке. Поэтому в околошовной зоне могут образовываться метастабильные хрупкие структуры мартенсита и холодные трещины. Чтобы создать в свариваемом металле условия, при которых околошовная зона охлаждалась бы со скоростью, не превышающей допустимую, применяют предварительный подогрев изделия. Температуру подогрева и режим сварки определяют соответствующим расчетом. Обычно температура подогрева хромо-молибденовых жаропрочных сталей лежит в пределах 200 — 300 °С. После сварки все изделия из жаропрочных низколегированных сталей подвергают термической обработке (чаще — нормализации с отпуском, иногда — высокому отпуску для выравнивания структуры и снятия сварочных напряжений).
Низколегированные конструкционные
Стали (25ХГСА, ЗОХГСА, 35ХМ и др.), наиболее широко применяемые в машиностроении, используют преимущественно в термически обработанном виде. Такие стали обладают высокими механическими свойствами, в особенности прочностными характеристиками (σв = 80 ÷ 110 кГ/мм2).
Свариваемость низколегированных сталей значительно хуже, чем сталей ранее рассмотренных групп, что связано с повышенной склонностью металла шва и околошовной зоны к образованию трещин. Свариваемость этих сталей имеет много общих черт со свариваемостью среднелегированных сталей перлитного класса.
Техника Безопасности и Охрана труда
при выполнении сварочных работ
Рабочее место сварщика должно содержаться в чистоте и порядке, не допуская ничего лишнего, мешающего работе на рабочем месте, а также в проходах и проездах. Детали и заготовки следует держать в устойчивом положении на подкладках а стеллажах, высота штабелей не должна превышать полторы ширины или полтора диаметра основания штабеля и во всех случаях не должна быть более 1 м.
Сварочные кабели нельзя располагать рядом с газосварочными шлангами и трубопроводами, находящимися под давлением, или по участкам с высокой температурой, а также вблизи кислородных баллонов и ацетиленовых генераторов.
Не должны производиться сварка и резка внутри сосудов с закрытыми люками или невывернутыми пробками, у неогражденных или незакрытых люков, проемов, колодцев и т. п..
Сварщики, работающие на строительных площадках, обязаны носить каски, предохраняющие голову рабочего от возможного травмирования падающими предметами и защищающие от ударов поражения электрическим током и атмосферных воздействий. Под каску должен одеваться головной убор — подшлемник. Важными средствами индивидуальной защиты сварщика являются спецодежда и спец-обувь. Спецодежда (куртки и брюки) изготовляется из материала, предохраняющего сварщика от излучения и имеющего противоискровые нашивки. Для работы в стационарных постах сварщик использует фартук, предохраняющий от брызг, особенно опасных при дуговой резке. Обувь сварщика, работающего на монтажной площадке, должна быть с нескользящей подметкой.
При использовании материалов, выделяющих повышенное количество сварочных аэрозолей (цветных металлов и сталей с цинком и цинковым покрытием и др.), применяют усиленную вентиляцию, обеспечивающую подачу чистого воздуха к сварщику. Однако общая вентиляция не всегда достигает нужного эффекта, поэтому прибегают к средствам индивидуальной защиты. Для этого в основном используют фильтрующие противопылевые респираторы и реже — изолирующие шланговые и автономные дыхательные аппараты. Необходимо отметить, что работа с использованием респиратора или противогаза вызывает быструю утомляемость рабочего, поэтому в каждом случае следует подобрать наиболее эффективный способ защиты.
Для снижения концентрации вредных веществ на рабочих местах до предельно допустимой необходимо применять отсосы различных типов.
В рабочем сечении панели скорость воздуха составляет 0,15 м/с, чго обеспечивает подвижность воздуха в зоне сварки на расстоянии не более 0,7 м от отсоса 0,5 м/с.
При сварке под слоем флюса применяется местный отсос, который подсоединен к шланговому полуавтомату.
При сварке в углекислом газе применяют местный отсос, совмещенный с автоматической или полуавтоматической горелкой.
При выполнении сварочных работ возникают опасные и вредные производственные факторы, которые могут привести к травме или профессиональным заболеваниям.
Опасный производственный фактор — это фактор, воздействие которого иа работающего приводит к травме.
Вредный производственный фактор — это фактор, воздействие которого на работающего приводит к заболеванию.
При сварке и резке медно цинковых сплавов и оцинкованных сталей происходит выделение окиси цинка, которая в процессе воздействия на организм работающего проявляется в виде сладковатого привкуса во рту, потери аппетита, жажды, повышенной утомляемости и сухого кашля.
Перечисленные признаки нарушения функционального состояния организма приводят к приступам лихорадки (озноб, повышение температуры, тошнота, рвота).
При сварке и резко свинца и металла, покрытого свинцовыми красками, происходит выделение окиси свинца, которая в процессе воздействия на организм работающего проявляется в виде металлического привкуса во рту, отрыжки, потери аппетита и упадка сил.
Перечисленные признаки нарушения функционального состояния организма приводят через 2,5—3,5 мес. к появлению лилово-серой каймы вокруг десен и сильным головным болям.
Безопасность труда на территории предприятия и цеха
На каждом предприятии действуют специальные правила техники безопасности. Движение любого вида транспорта и людей регулируется дорожными знаками и сигнальными устройствами, устанавливаемыми в соответствии с действующими правилами. Цеха связанные с возникновением особо резкого шума (с уровнем более 90 дБ, например при плазменно - дуговой резке), должны размещаться в изолированных зданиях.
Электробезопасность
Электротравмы возникают при прохождении электрического тока через тело человека.
Тяжесть поражения электрическим током зависит от величины тока и напряжения, а также от пути прохождения тока в организме человека, длительности действия тока, частоты (с повышением частоты переменного тока степень поражения снижается, переменный ток опаснее постоянного).
Помещения по степени опасности поражения людей электрическим током подразделяются на три категории: особо опасные (высокая влажность и температура воздуха, химически активная среда, приводящая к разрушению изоляции токоведущих частей), с повышенной опасностью (токопроводящие полы, возможности прикосновения человека к металлическим конструкциям и корпусам электрооборудования и др.) и без повышенной опасности (отсутствуют опасности поражения электротоком).
Пожарная безопасность
Причинами, вызывающими пожары в цехах, являются наличие легковоспламеняющихся веществ и горючих жидкостей, сжиженных горючих газов, твердых сгораемых материалов, емкостей и аппаратов с пожароопасными продуктами под давлением, электроустановок, вызывающих в процессе их работы электрические искры и др.
В целях предотвращения пожаров запрещается пользоваться сварщиком одеждой и рукавицами со следами масел, жиров, бензина, керосина и других горючих жидкостей; выполнять термическую резку и сварку свежеокрашенных конструкций до полного высыхания краски; выполнять сварку аппаратов, находящихся под электрическим напряжением, и сосудов, находящихся под давлением; производить без специальной подготовки резку и сварку емкостей из- под жидкого топлива и др.
Для тушения пожаров водой в большинстве производственных и общественных зданий на внутренней водопроводной сети установлены пожарные краны. Пена представляет собой концентрированную эмульсию двуоксида углерода, азота, дымовые газы и др.
Каждый сварочный пост должен иметь огнетушитель, бочок или ведро с водой, а также ящик с песком и лопатой. После окончания сварочных работ необходимо проверять рабочее помещение и зону, где выполнялись сварочные работы.
Принципы охраны окружающей среды
Охрана окружающей среды осуществляется на основе соблюдения следующих основных принципов:
1) приоритета охраны жизни и здоровья человека, настоящего и будущих поколений;
2) недопущения необратимых последствий загрязнения атмосферного воздуха для окружающей среды;
3) государственного регулирования выбросов вредных (загрязняющих) веществ в атмосферный воздух и вредных физических воздействий на него;
4) гласности, полноты и достоверности информации о состоянии атмосферного воздуха, его загрязнении;
5) научной обоснованности, системности и комплексности подхода к охране атмосферного воздуха и охране окружающей среды в целом.
Юридические лица, имеющие источники выбросов вредных (загрязняющих) веществ в атмосферный воздух, а также вредного физического воздействия на атмосферный воздух, которые превышают установленные для них нормативы предельно допустимых выбросов, осуществляют согласованные с территориальными подразделениями уполномоченного государственного органа в области охраны атмосферного воздуха мероприятия по его охране в целях достижения норм предельно допустимых выбросов.
Мероприятия по охране атмосферного воздуха должны проводиться в соответствии с законодательством Республики Казахстан в области охраны атмосферного воздуха.
Проекты программ охраны атмосферного воздуха выносятся на обсуждение граждан и общественных объединений в целях учета их предложений при планировании и осуществлении мероприятий по улучшению качества атмосферного воздуха. Финансирование программ охраны атмосферного воздуха и мероприятий по их осуществлению проводится в соответствии с законодательством Республики Казахстан.
В целях определения критериев безопасности и (или) безвредности воздействия химических, физических, биологических и радиационных факторов на людей, животных и растения, особо охраняемые природные территории и иные объекты, а также в целях оценки состояния атмосферного воздуха устанавливаются экологические нормативы качества атмосферного воздуха и предельно допустимые уровни физических воздействий.
В целях государственного регулирования выбросов вредных (загрязняющих) веществ в атмосферный воздух устанавливаются удельные нормативы выбросов и нормативы предельно допустимых выбросов.
Удельные нормативы выбросов устанавливаются уполномоченным государственным органом в области охраны атмосферного воздуха по согласованию с соответствующим государственным органом, в компетенцию которого входит разработка технологических нормативов охраны атмосферного воздуха для отдельных видов стационарных источников выбросов вредных (загрязняющих) веществ в атмосферный воздух, а также для являющихся источниками загрязнения атмосферного воздуха транспортных или иных передвижных средств.
В целях государственного регулирования вредных физических воздействий на атмосферный воздух устанавливаются предельно допустимые нормативы вредных физических воздействий на атмосферный воздух.
Нормативы выбросов вредных (загрязняющих) веществ в атмосферный воздух и предельно допустимые нормативы вредных физических воздействий на атмосферный воздух, методы их определения и виды источников, для которых они устанавливаются, разрабатываются и утверждаются в порядке, определенном Правительством Республики Казахстан.
Заключение
Первые попытки применения для сварки и резки горючих газов в смеси с кислородом относятся к началу ХХ-го века. Созданию газовой сварки и резки способствовали исследования процессов горения газовых смесей французским ученым Анри Луи Ле Шателье. В 1895 г. он доложил французской академии наук о получении им высокотемпературного пламени (свыше 3000о С) при сжигании ацетилена и кислорода. Ацетилен был открыт еще в 1836г., а в 1863г. был синтезирован М. Бертло. Однако доступным техническим продуктом стал лишь после того, как в первой половине 90-х годов XIX века химики Муассан во Франции и Вильсон в Америке нашли способ приготовления карбида кальция из известняка и угля.
Первую ацетилено-кислородную сварочную горелку сконструировали французские инженеры Эдмон Фуше и Шарль Пикар, которые получили на нее патент Германии в 1903 году. Предложенные ими конструкции газосварочных горелок принципиально почти не изменились до настоящего времени.
В 1904г. во Франции была обнаружена возможность использования ацетилено-кислородной горелки для резки металлов, а в 1908 - 1909гг. во Франции и в Германии были проведены первые успешные опыты по кислородной подводной резке. В последующие 5 - 9 лет было получено несколько патентов в этой области и разработаны промышленные конструкции резаков для подводной резки.
В начале ХХ в. газовая сварка и резка в России использовалась весьма ограниченно при ремонте изделий из низкоуглеродистой стали, меди и чугуна на ряде заводов. При этом использовалась аппаратура и материалы, ввозимые из-за границы. Начало промышленного производства газосварочной аппаратуры в СССР относится к 1927 - 1928гг.
В течение 1933 - 1934гг. окончательно прекратился ввоз автогенной аппаратуры. К этому же времени относятся крупные исследования в области автогенной сварки и резки Н.Н. Клебанова, работы которого сохранили большое значение до настоящего времени.
После того как в технику дуговой сварки начали широко внедряться толстопокрытые электроды, появились новые способы дуговой сварки, разработаны совершенные и высокопроизводительные машины для контактной сварки, газовая сварка постепенно начала вытесняться на многих производствах электрической сваркой. Теперь на первое место выдвигается кислородная резка. В 30-х годах широкое распространение получила резка с использованием жидких горючих, главным образом керосина. К этому периоду относится и возникновение механизированной кислородной резки. Новый всплеск развития газопламенной обработки металлов приходится на период второй мировой войны и послевоенные годы. В послевоенные годы создана специальная отрасль промышленности - автогенное машиностроение, в рамках которой был построен одесский завод «Автогенмаш», начавший выдавать продукцию в 1952г. На Воронежском экспериментальном заводе автогенного машиностроения, ранее производивший кислород и ацетилен, был организован выпуск ацетиленовых генераторов и оборудования для получения растворенного ацетилена. Позднее автогенную аппаратуру начал выпускать Кироваканский завод автогенного машиностроения, также построенный в рамках отрасли автогенного машиностроения.
Период после 50-х годов особенно интенсивно развивается механизация и автоматизация процессов резки металла. Весьма бурно развиваются механизация и автоматизация процессов газопламенной обработки металлов, в первую очередь это касается процессов газокислородной резки. широко начинают использоваться газорезательные машины с числовым программным управлением. Они позволяют производить высокоточную резку под сварку и механообработку заготовок любой конфигурации и сложности, с постоянной повторяемостью размеров и минимальными отклонениями этих размеров от номинала, а также чистотой поверхности реза, сопоставимой с этими же параметрами при механообработке.
Кислородная резка, несмотря на некоторые ограничения, и сегодня остается одним из основных процессов газопламенной обработки. Процесс резки легко поддается механизации и автоматизации. Машины для кислородной резки могут резать углеродистые стали толщиной до 300 мм несколькими резаками, в том числе и V- или Х-образной подготовкой кромок под сварку с одновременной резкой. Они дешевле плазменных и лазерных и более просты в обслуживании. Некоторые специальные машины, например для металлургического производства, позволяют производить резку сталей толщиной до 1200мм.
Процесс резки легко поддается механизации и автоматизации. Машины для кислородной резки могут резать углеродистые стали толщиной до 300 мм несколькими резаками, в том числе и V- или Х-образной подготовкой кромок под сварку с одновременной резкой. Они дешевле плазменных и лазерных и более просты в обслуживании. Некоторые специальные машины, например для металлургического производства, позволяют производить резку сталей толщиной до 1200мм.
оборудование для ручной газовой резки можно классифицировать следующим образом.
Несмотря на кажущуюся простоту процесса, далеко не все металлы поддаются газокислородной резке. Это, в первую очередь, связано с тем, что у большинства металлов температура плавления ниже температуры воспламенения в кислороде, что и приводит к невозможности процесса резки. Кроме того, препятствием на пути этого процесса зачастую становится высокая температура плавления окислов металла, их недостаточная жидкотекучесть, высокая теплопроводность металла и др. факторы.
Эти ограничения привели к появлению новых, более концентрированных, чем газовое пламя, источников нагрева. Возникают процессы газоэлектрической, плазменной, электронно-лучевой и (в 70-х годах) газолазерной резки. Осваиваются способы обработки неметаллических материалов высокотемпературной порошково-кислородной и термореактивной струями газа. Это обусловило появление в технической литературе вместо собирательного термина «газовая» или «огневая» резка, охватывающего различные процессы кислородной резки, нового, объединяющего названия - «термическая» резка, принятого Международным институтом сварки.
Но учитывая, что абсолютное большинство конструкционных сталей, т.е. металлов, которые в основном и подвергаются процессу термической резки, относятся к классу низкоуглеродистых или низколегированных, на которые перечисленные выше ограничения не распространяются, становится ясно, почему среди всех процессов термической резки по объему выполняемых работ газокислородная резка стоит на первом месте.
до тех пор, пока человечество не изобрело более мобильного, экономичного и менее энергоемкого процесса термической резки, чем газокислородная, этот процесс будет занимать лидирующее место среди всех процессов термической резки.
СПИСОК ЛИТЕРАТУРЫ
1. Сварка в СССР. Том первый. Издательство «Наука». Москва 1981
2. История техники. Зворыкин и др.
3. Большая Советская энциклопедия.
4. «Дуговая и газовая сварка» В.М.Рыбаков, МОСКВА«Высшая школа»
1986 г.
5. «Электросварщик» В.Л. Цегельский, ПРОФТЕХИЗДАТ 1960 г.
6. «Дуговая сварка» А.М. Китаев, Я.А. Китаев, МОСКВА «Машиностроение» 1983 г.
42